I finally finished a project, a tissue box cover made of oak. This project was suggested to me by my wife as a birthday gift for my sister-in-law. I liked the idea so I got right to work on the design. I decided to use 1/4" red oak for the sides and 1/2" red oak for the top. I also personalized the project by adding a Celtic knot design to the front panel and two age-related quotes to the left and right sides of the tissue box.
Project Design: I used SketchUp to make some technical drawings of the basic design.
Step 1. My first step was to draw the three dimensional shape of the tissue box. This provided me with a reference for sizing the project.
Step 2. I then created properly sized panels for each side. Since I did not want any seams visible from the front, I made the front panel wide enough to cover the end gran of the sides. The side panels I made long enough to cover the end grain of the rear panel.
Step 3. Create the box cover panel. This panel was designed to overhang the sides by 1/4". The bottom surface of the cover panel is milled 1/8" to fit the top of the width and depth of the assembled side panels.
Step 4. Create a cut list from the SketchUp drawing.
Artwork Design: Since I used my CNC router to carve the artwork, I used ArtCam Express as the design platform. I still consider myself a novice when it comes to using both ArtCam and my CNC. I have found that following these basic steps produces satisfactory results.
Step 1. Find a suitable photograph or drawing for the carving. I found photographs for the Celtic knot and illustrations of the two quotes to carve into the sides.
Step 2. Create vectors from the artwork. ArtCam has the ability to automatically create vectors from standard photos. I will not describe the entire process here.
Step 3. Adjust and correct any deficiencies in the created vectors. ArtCam provides tools to help fix any vectors that prevent proper machining of the design. I also created a vector to cut out the oval hole on the top of the tissue box and rectangular vectors defining the outside of the cover.
Step 4. Once satisfied with the vectors, export them as an .eps file.
Shopping: Once I completed the above steps, I took a trip to the local lumber store to find the wood for the project. Getting back home, it was time to head to the workshop.
Get to Work: My shop is in the garage. I have a single car garage that not only serves as my shop, but as a household storage area. In the winter, we also store those summertime items like garden hoses, lawn chairs, etc. As a result, the shop is pretty crowded. I have a table saw, drill press, planer, band-saw and CNC router. Of these, only the band saw and CNC router are fixed base. The shop is sometimes pretty cold during the winter. Because of this, I often do my measuring and layout in the house. That's what I did for this project.
The actual work on the project consisted of the following steps:
1 - Measure & Layout. I laid out the measurements with the wood grain running vertically. I measured and marked the dimensions for each box side on the oak panel leaving space for the saw blade kerf. For the top, I first had to edge join three pieces of narrow stock. I measured and marked the narrow stock 2" longer than needed for the top. I used this excess to clamp the board down during CNC milling.
2 - Prepare the blank for the top. To the shop! I cut the narrow stock on the table saw. I then edge-glued and clamped the three pieces of narrow stock to make the blank for the top.
3 - Cut side panels to size. I cut the 1/4" stock as marked to make the four side panels.
4 - V-carve side panels. I secured the side panel stock to my CNC table after marking the center point of the panel face. I installed my Dremel with a 0.005" 60 deg. v-bit into the CNC fixture. I selected this bit to provide a nice, detailed carving. I then located the CNC "working zero" to the center point of the side panel. Once this was done, I ran the CNC program for the side being carved.
5 - Mill bottom of cover. I marked the center point of the cover blank. After securing the blank to the CNC table, I centered the working zero and ran the cut program using a 1/4" end mill.
6 - Mill top of cover. I flipped the cover over to mill 1/8" from the entire surface of the cover. This was also cut using the 1/4" end mill.
7 - Cover cuts. First the hole in the cover was cut out using the CNC with a 1/4" end mill. Then, the cover was cut to its final size using the CNC and 1/4" end mill.
8 - Round over cover edges. The edges of the cover were rounded over using a 1/4" round over bit as were the edges of the oval hole in the cover. This produce a nice smooth surface.
9 - Sand parts. All pieces were sanded with particular attention given to the v-carvings. Once satisfied, the parts were wiped down to remove any remaining dust.
9 - Glue together. For gluing, I used a new tissue box to provide support and maintain squareness of the project. I used waxed paper to prevent gluing the project to the tissue box. I did the gluing in stages. First, I glued the side panels to the back panel. I used clamps to hold the parts in place while the glue set up. Once that was done, I glued the front panel to the assembly and clamped it until dry. I then glued to top to the completed box assembly.
10 - Finish. For a finish, I used a natural paste wax. I rubbed in 3 coats leaving each coat to dry a few hours before the next coat. Once the last coat was applied, I hand polished using a soft cloth. I also removed excess wax that had built up in the carvings using toothpicks and an old toothbrush.
I am reasonably satisfied with the final project. In future projects with small text, I plan to experiment with other engraving bits to get a cleaner finish.
That's it for now. Hope you enjoyed this post.
Peace.
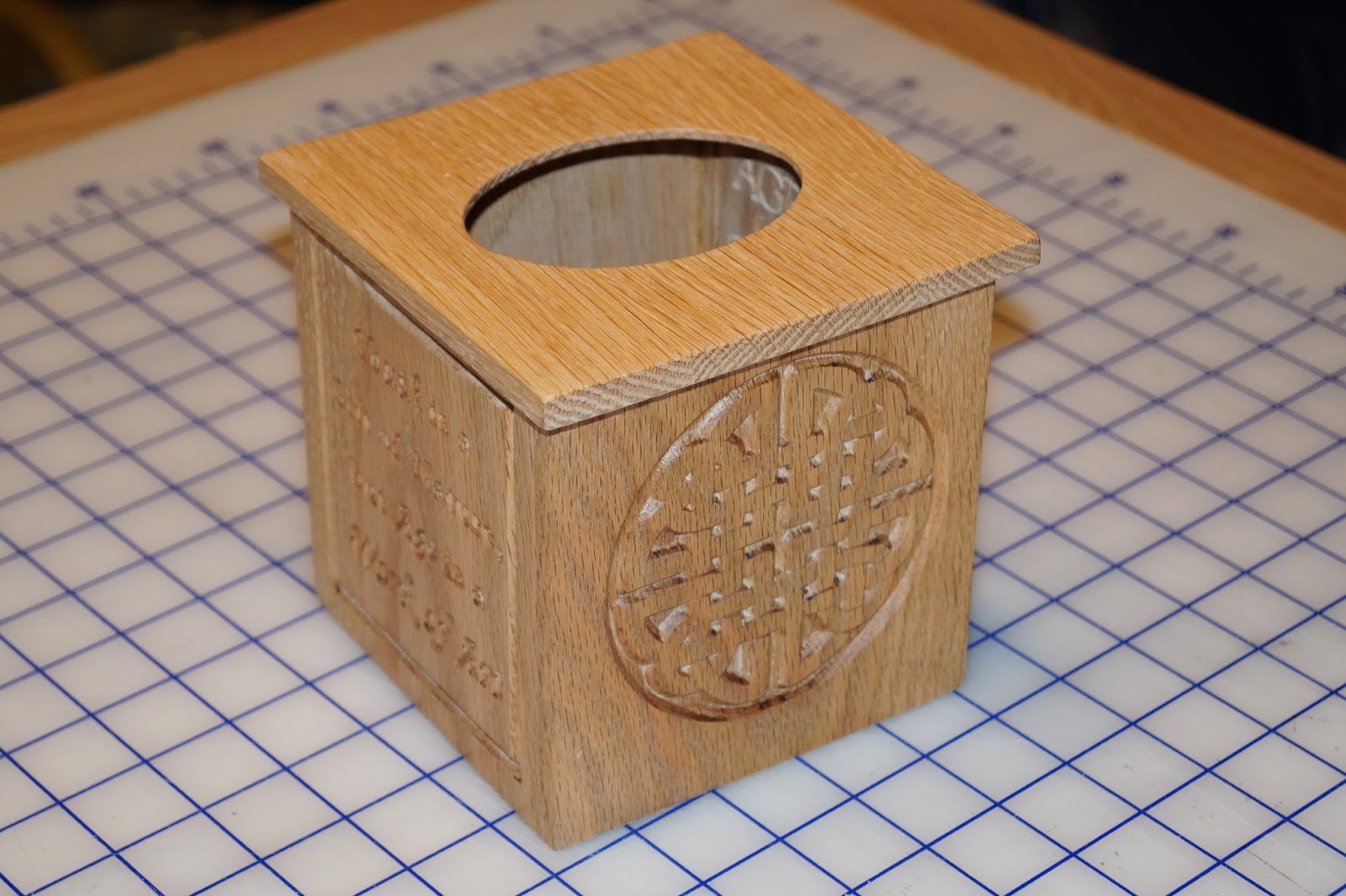 |
Finished Tissue Box Cover |
 |
The Celtic Knot on the front panel. |
 |
"Youth is a Gift of Nature, but Age is a Work of Art." |
 |
"Age is merely the number of years the world has been enjoying you." |
 |
The template for creating the vectors to cut the top cover hole was a used tissue box. |